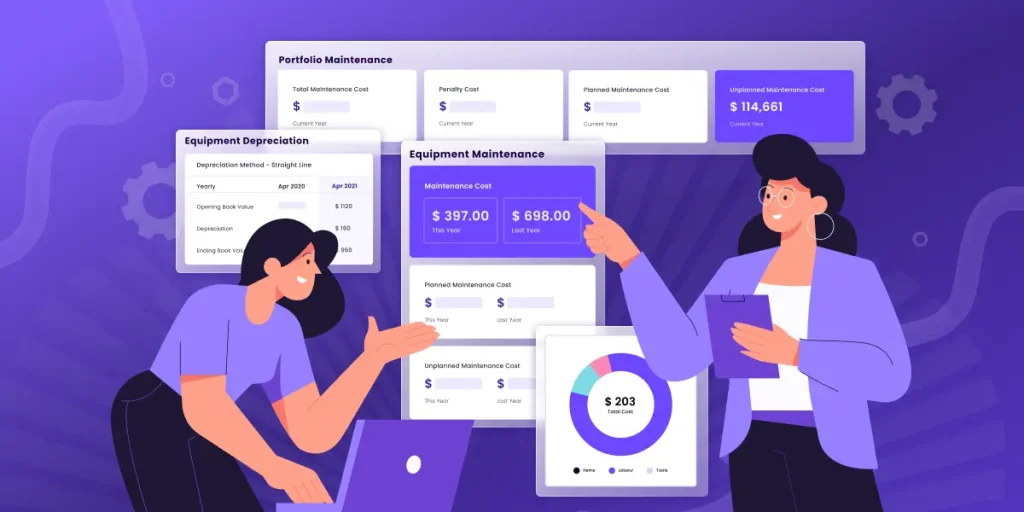
Planned Preventive Maintenance (PPM) is a proactive approach to building and asset upkeep. By scheduling regular maintenance checks, UK businesses and organisations can reduce the risk of equipment failure, ensure compliance with regulations, and extend the life of vital systems.
But a common question arises: how often should PPM be carried out? The answer varies depending on the type of equipment, industry standards, and legal requirements. This article provides a clear guideline on PPM frequency for key systems in UK facilities.
Why Frequency Matters in PPM
Establishing the right frequency for PPM tasks is essential for three main reasons:
- Compliance with UK regulations (such as health and safety, fire safety, and building standards)
- Preventing costly downtime and emergency repairs
- Maximising efficiency and extending equipment lifespan
Too frequent servicing can be unnecessarily costly, while infrequent maintenance increases risk. A balanced schedule ensures optimal performance without waste.
Frequency Guidelines by System Type
Below is a breakdown of recommended maintenance intervals for common building systems and equipment in the UK:
1. Fire Alarm and Detection Systems
PPM Frequency:
Every 6 months
Details:
Testing, inspection, and servicing are mandatory to ensure compliance with fire safety regulations.
2. HVAC (Heating, Ventilation & Air Conditioning)
PPM Frequency:
Quarterly to biannually, depending on usage
Details:
Systems should be checked for filter changes, refrigerant levels, duct cleanliness, and mechanical wear. Heavy-use systems may need quarterly checks.
3. Emergency Lighting
PPM Frequency:
Monthly function tests and a full annual test
Details:
Ensures lighting operates in a power outage and meets evacuation standards.
4. Lifts and Elevators
PPM Frequency:
Every 6 months (commercial), every 3 months (passenger lifts in high-traffic buildings)
Details:
Regular inspections prevent breakdowns and ensure legal safety compliance.
5. Water Systems (Legionella Risk)
PPM Frequency:
Varies by risk assessment; typically, monthly checks and annual reviews
Details:
Essential for Legionella prevention and compliance with HSE guidance.
6. Electrical Installations
PPM Frequency:
Every 5 years (commercial), with annual visual checks
Details:
A Full Electrical Installation Condition Report (EICR) is legally recommended every five years.
7. Fire Extinguishers
PPM Frequency:
Annually
Details:
Inspection and servicing ensure readiness during an emergency.
Factors Influencing PPM Schedules
While guidelines provide a baseline, actual maintenance frequency should also consider:
- Manufacturer recommendations
- Equipment age and condition
- Building usage and footfall
- Environmental factors (e.g., exposure to moisture, dust, temperature extremes)
A high-traffic retail facility will need more frequent checks than a small office with low usage.
Creating a PPM Schedule That Works
To ensure nothing is missed:
- Use a Computerised Maintenance Management System (CMMS)to automate reminders and records.
- Carry out a detailed site audit to list all assets and set a frequency based on need.
- Review the plan annually to adjust frequencies based on usage, wear, and incidents.
Conclusion
PPM is not a one-size-fits-all solution, but having a reliable schedule tailored to your facility is critical. By aligning maintenance frequencies with UK standards and real-world conditions, businesses can reduce risk, comply with the law, and protect their investments.
Need help implementing the right PPM strategy? Consider consulting facilities management professionals who can design a schedule based on your building’s specific needs and regulatory obligations.